Laser Cutting: Revolutionizing Rapid Prototyping and Small-Scale Manufacturing
- Rabbit Laser USA
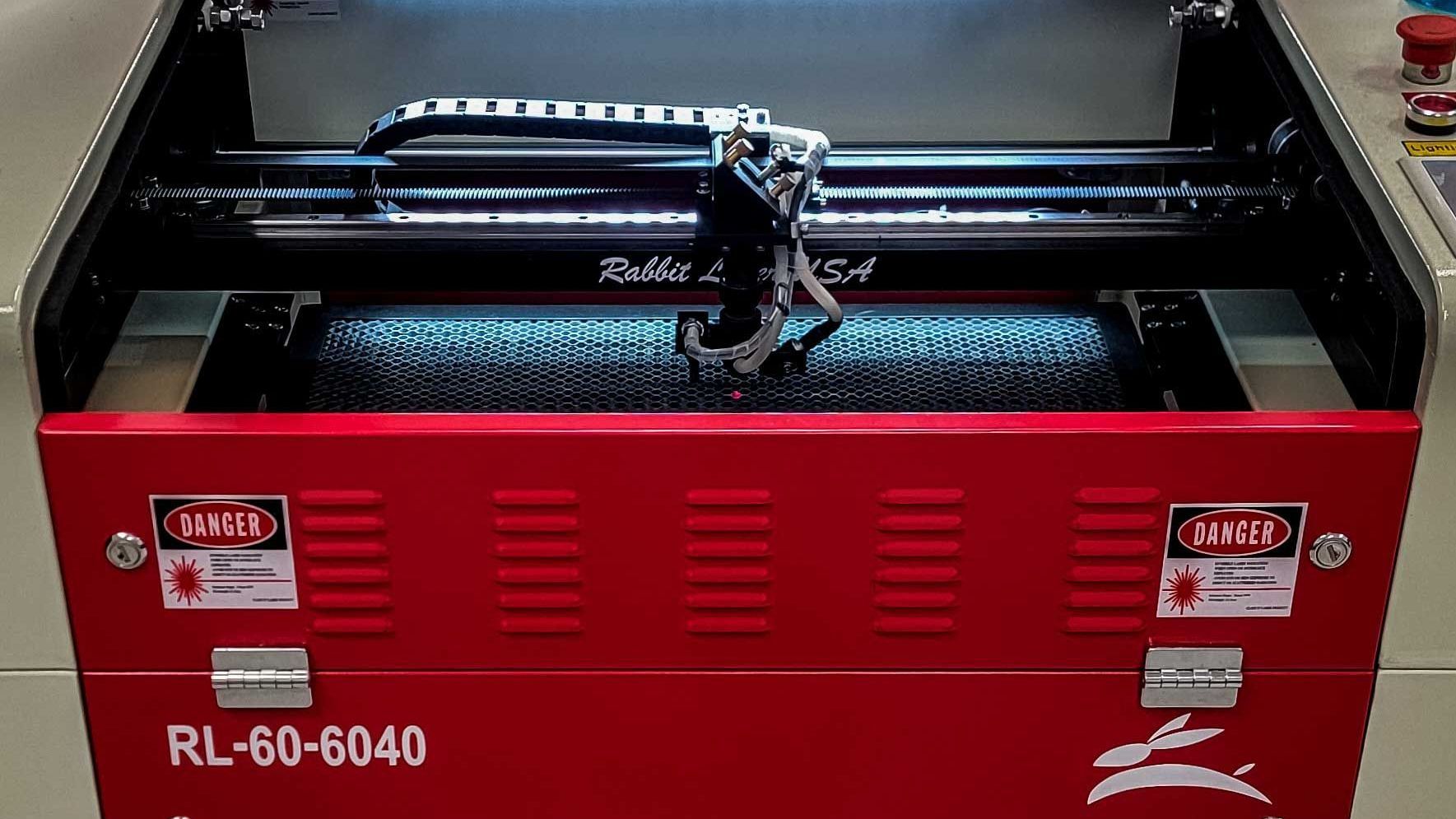
Laser cutting has emerged as a game-changer in the realm of rapid prototyping and small-scale manufacturing. This innovative technology has revolutionized traditional manufacturing processes with its exceptional efficiency, unparalleled accuracy, and remarkable material versatility. In this article, we delve into the multifaceted world of laser cutting, uncovering its vital role in transforming ideas into tangible prototypes and driving the evolution of small-scale manufacturing.
The Power of Laser Cutting in Rapid Prototyping
Rapid prototyping is the cornerstone of product development, enabling designers and engineers to iterate quickly and bring their concepts to life. Laser cutting plays a pivotal role in this process, offering a precise and swift method to transform digital designs into physical prototypes. By harnessing the focused energy of a laser beam, intricate patterns and complex geometries are meticulously etched onto various materials, ensuring a faithful representation of the intended product.
Efficiency Redefined
In the realm of rapid prototyping, time is of the essence. Laser cutting excels in this aspect by significantly reducing the production timeline. Traditional methods often involve cumbersome tool changes and intricate setups, causing delays in the iterative cycle. Laser cutting eliminates these bottlenecks, allowing for seamless transitions between design adjustments and physical realization. The efficiency of laser cutting expedites the journey from concept to prototype, giving innovators a competitive edge.
Unmatched Accuracy
Precision is non-negotiable in prototyping, where every millimeter can influence the final product's functionality. Laser cutting, driven by advanced computer-controlled systems, achieves levels of accuracy that were previously unattainable. The focused laser beam ensures minimal material wastage and negligible distortion, resulting in prototypes that mirror the digital design with exceptional fidelity.
Laser Cutting: A Catalyst for Small-Scale Manufacturing
Beyond rapid prototyping, laser cutting has emerged as a catalyst for innovation in the small-scale manufacturing landscape. The technology's prowess extends beyond prototypes, enabling the production of intricate, custom, and limited-run components with unprecedented efficiency and versatility.
Versatility Unleashed
One of laser cutting's standout features is its compatibility with an extensive range of materials. From metals and plastics to wood and fabrics, laser cutting adapts seamlessly, offering manufacturers the freedom to explore various mediums. This versatility is invaluable, particularly for niche industries and bespoke manufacturing, where each product may require distinct materials.
Streamlined Production
Small-scale manufacturing thrives on agility and adaptability. Laser cutting aligns perfectly with these principles by streamlining production processes. The absence of intricate setups and the need for complex tool changes simplifies the manufacturing workflow. As a result, manufacturers can pivot swiftly between different products, responding to market demands without compromising on quality or efficiency.
Embracing the Future
Laser cutting's influence on rapid prototyping and small-scale manufacturing is nothing short of transformative. Its efficient, accurate, and versatile nature has redefined how ideas evolve into tangible creations. As technology continues to advance, we can only anticipate further innovations in laser cutting, pushing the boundaries of what's possible in the realm of product development and manufacturing.
In conclusion, laser cutting has proven to be a cornerstone of innovation in both rapid prototyping and small-scale manufacturing. Its efficiency, accuracy, and material versatility have set new standards for the industry. As we look ahead, the collaboration between human ingenuity and laser technology holds the promise of even more remarkable advancements, driving the evolution of manufacturing processes to unprecedented heights. 🐇
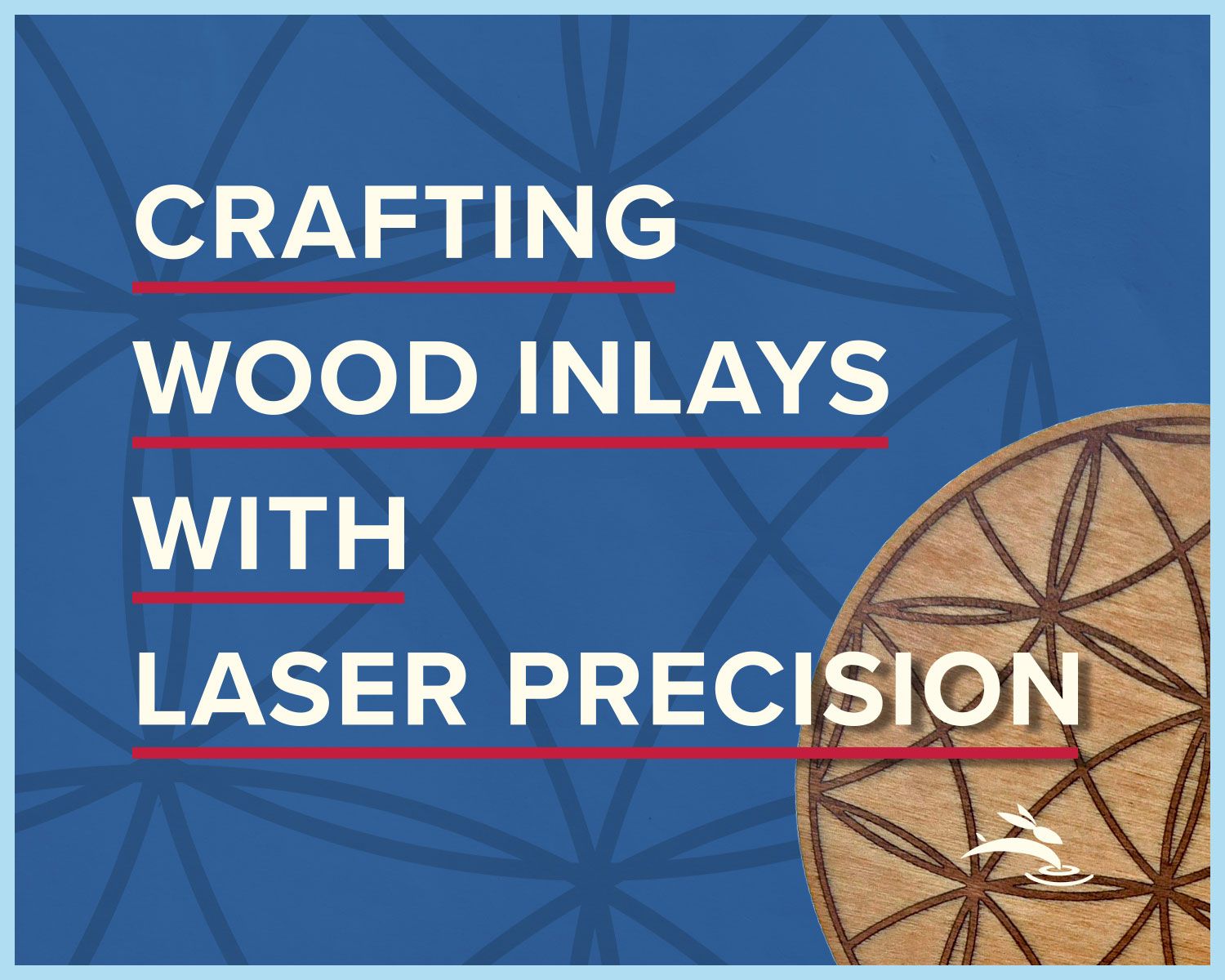
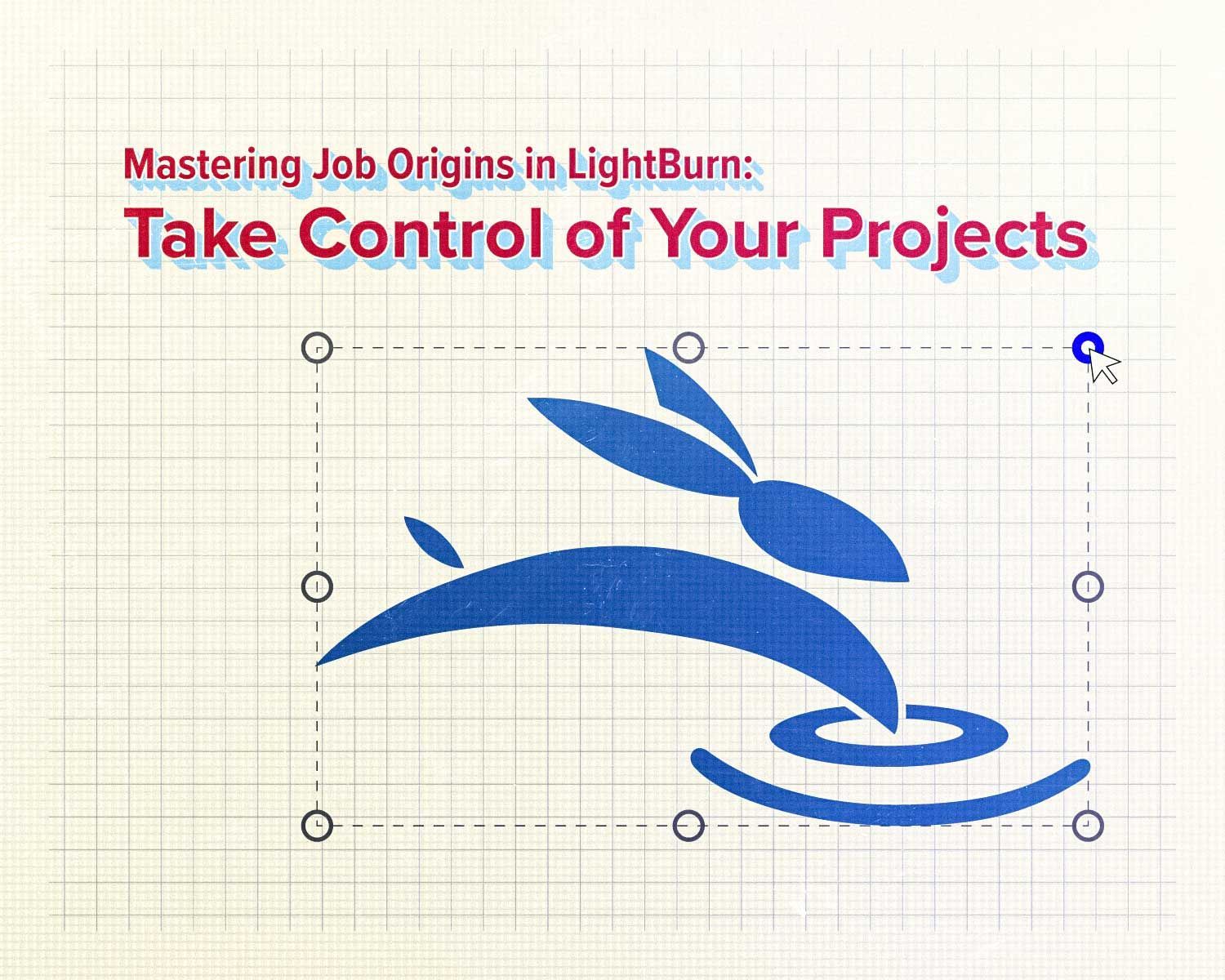
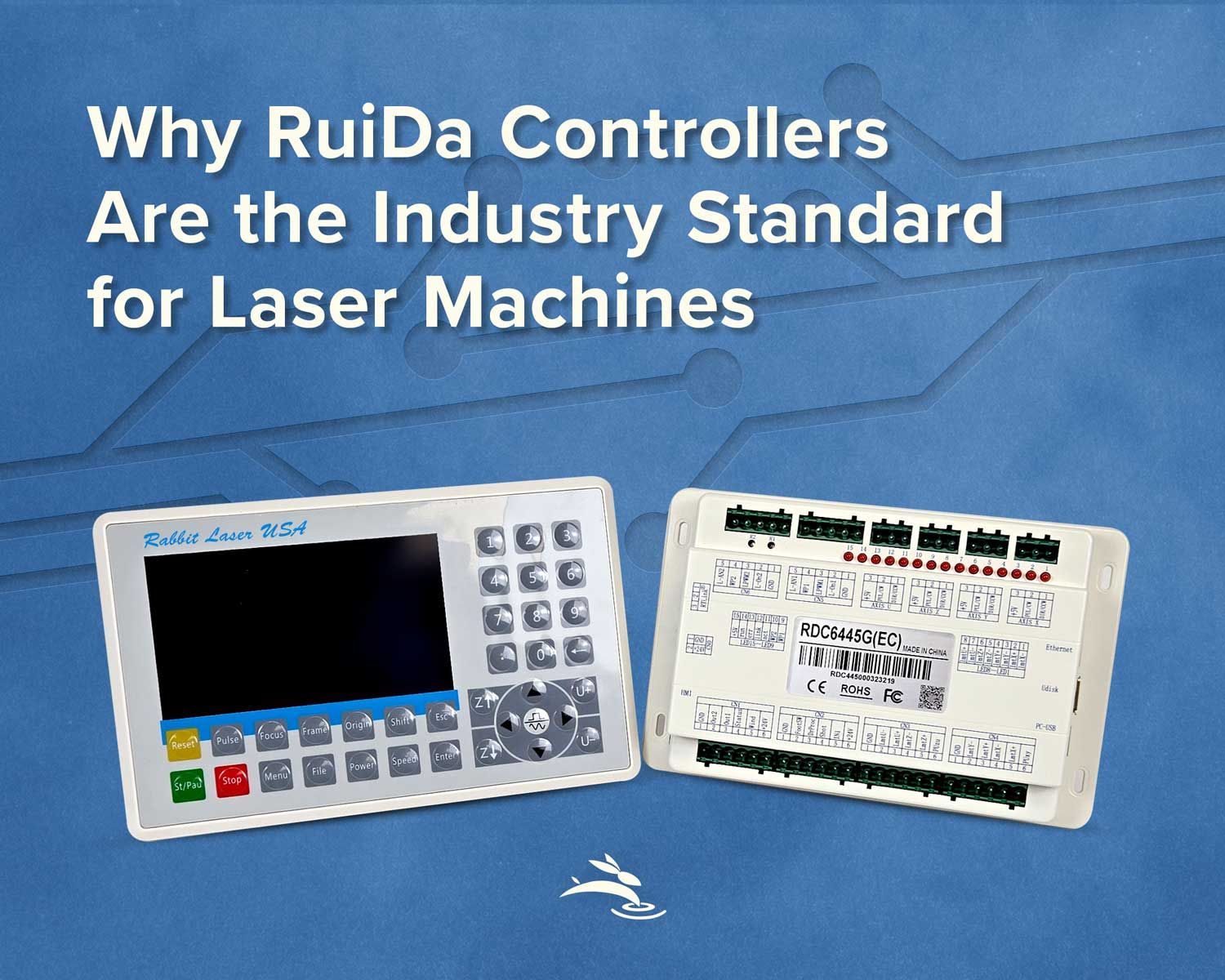
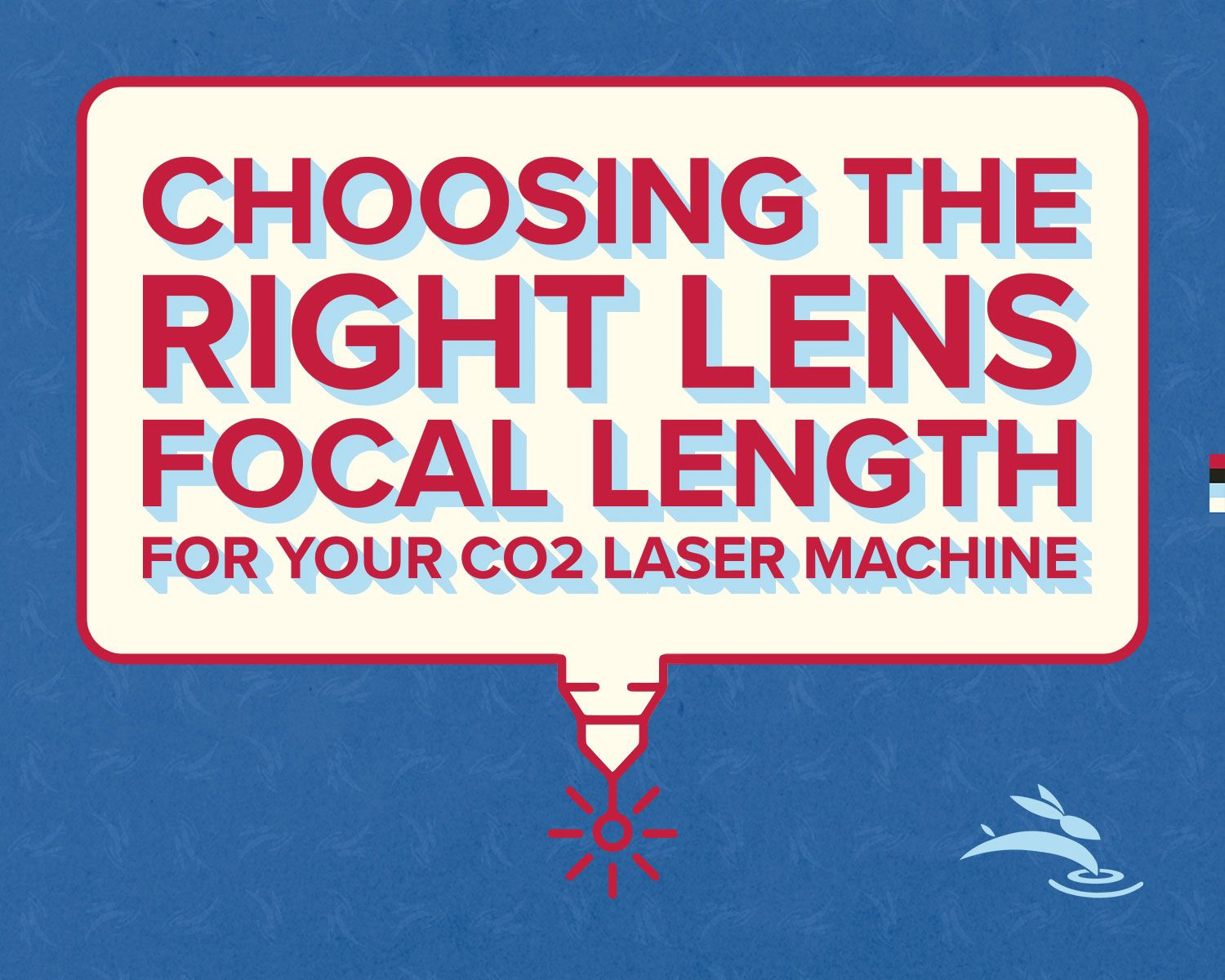
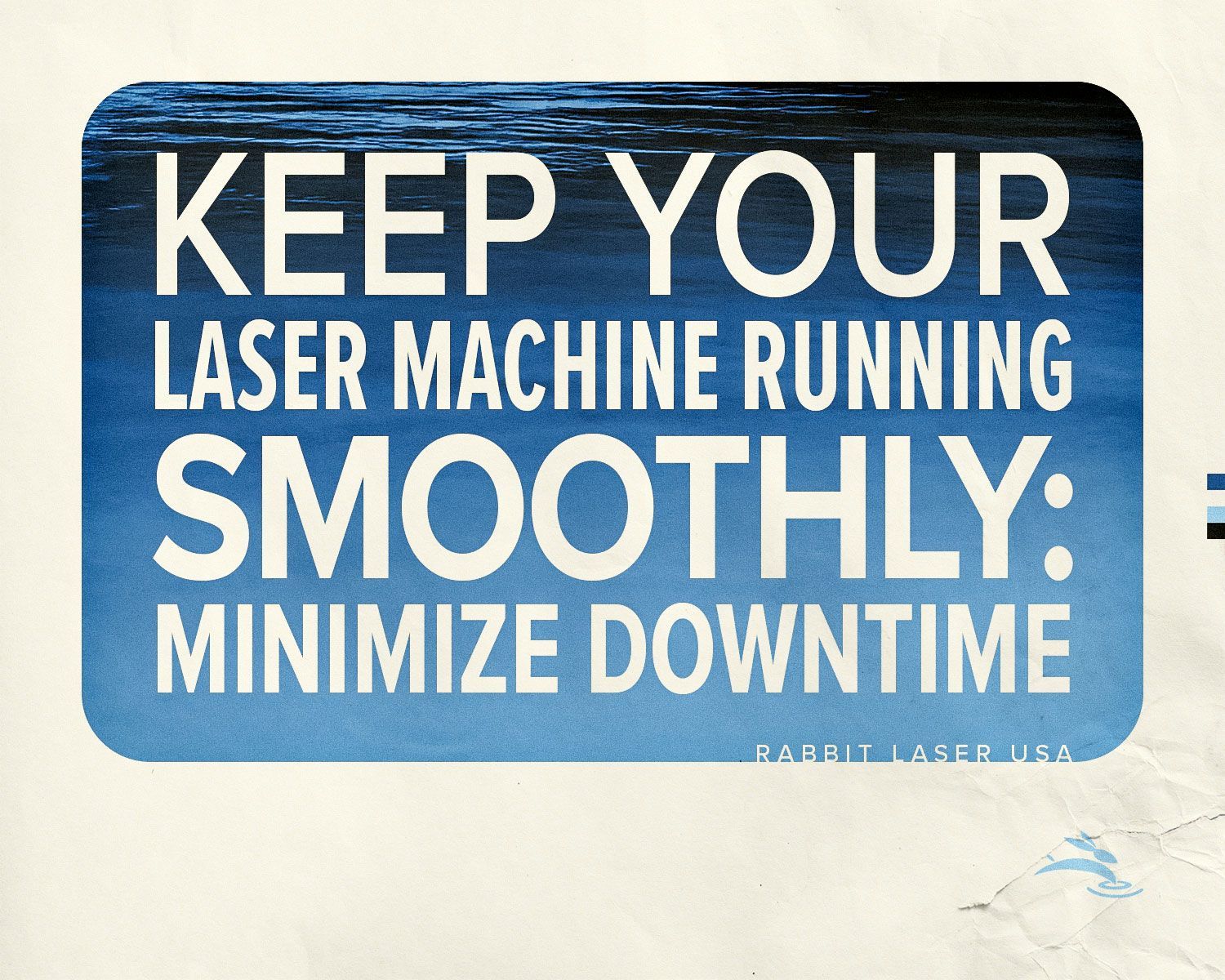
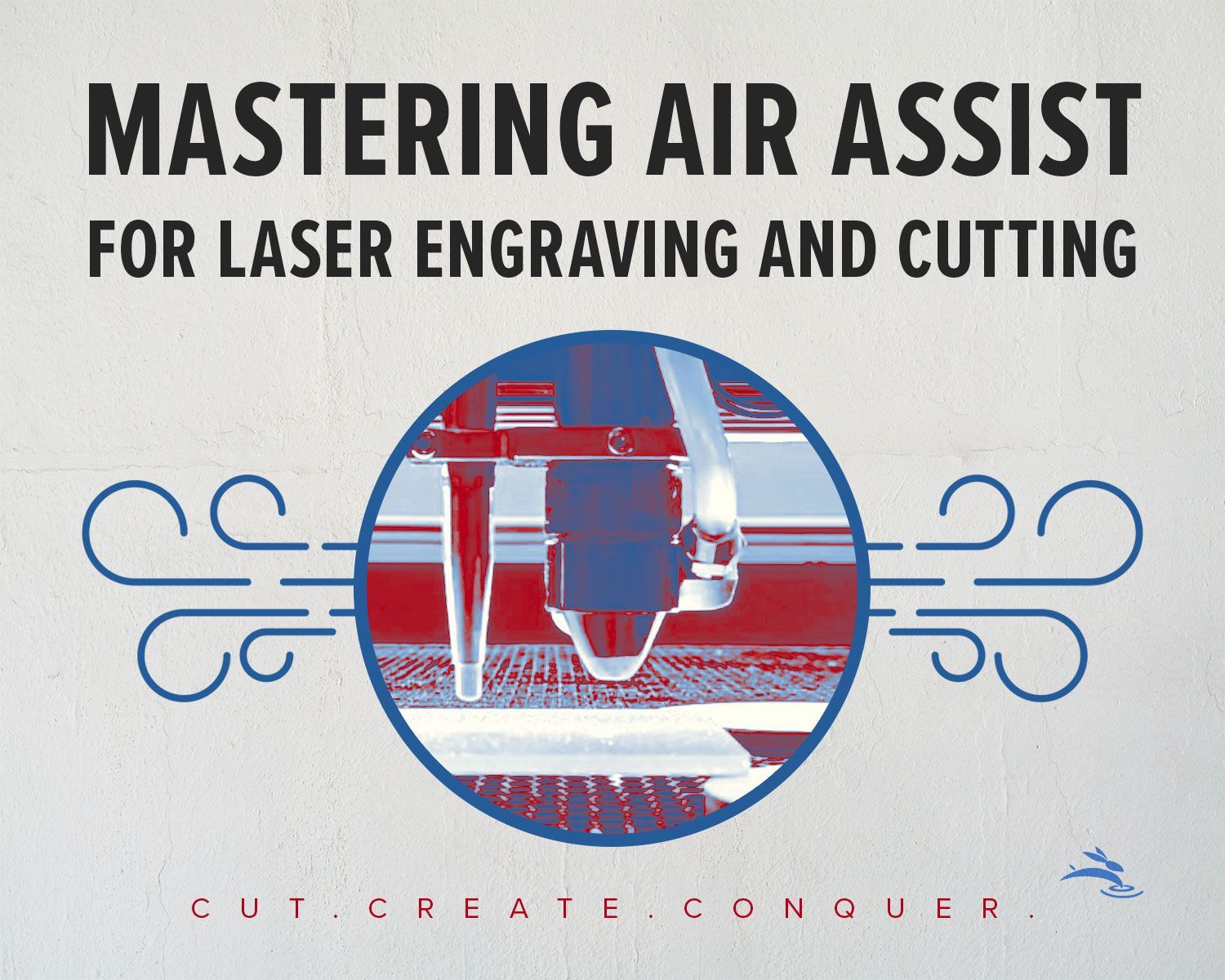